
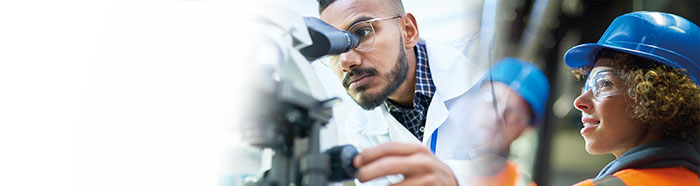
Research projects
- Research area
Big data and sensors and digitalisation for the offshore environment
- Institution
University of Sheffield
- Research project
Blade Factory Digital Twin for Recording and Analysing Production Parameters
- Lead supervisor
- PhD Student
- Supervisory Team
Professor James Gilbert (Director - Energy & Environment Institute, University of Hull)
Professor David Wagg (Professor of Nonlinear Dynamics, University of Sheffield)
Project Description:
In partnership with Siemens Gamesa Renewable Energy (SGRE), this PhD will develop a Blade Factory level Digital Twin. The PhD directly addresses sector needs to understand the application of digital twins to predict real world performance of turbine blade manufacturing processes.
Wind turbine blades are some of the largest composite structures currently manufactured and they are becoming larger and more sophisticated. Blades are manufactured in SGRE’s Hull facility through a number of complex manual and machine-based processes. In order to monitor and improve these processes a digital twin of them is required.
A digital twin is a digital representation of the processes and procedures within the manufacturing environment, displayed and modelled as close to real time as possible. As such, a digital twin is a very powerful tool which can be used to combine the many and complex data streams inside the factory environment into a single simulation; from that simulation, data can then be monitored to help improve machine or process efficiencies, reduce safety risks and make other general improvements.
Working with SGRE, the largest manufacturer of offshore wind turbines, you will investigate the end-to-end production process inside the Hull factory environment and identify the key aspects and data models that are needed to create the type of simulation that is desired. The work will involve close collaboration with SGRE colleagues in the UK and Denmark and with the University of Hull who are developing simulation models of specific manufacturing processes.
The project aims are:
- Identify all relevant parameters affecting the blade manufacturing process and further identify which of these could contribute to the digital twin simulation.
- Explore how to digitalise the data collection infrastructure of the manufacturing process while considering the connectivity of machinery and edge devices that might have a wide range capability when it comes to ‘built in connectivity’.