
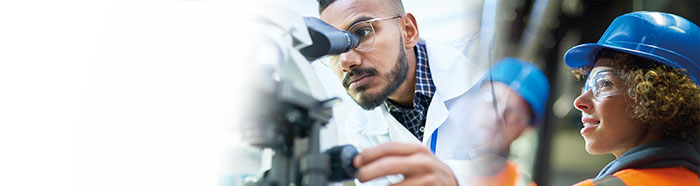
Research projects
- Research area
Physics and Engineering of the offshore environment
- Institution
Durham University
- Research project
Active wind farm control via morphing blade technology
- Lead supervisor
Dr Majid Bastankhah (Associate Professor, Department of Engineering, Durham University)
- PhD Student
- Supervisory Team
Dr Stefan Szyniszewski (Assistant Professor, Department of Engineering, Durham University)
Professor James Gilbert (Director - Energy & Environment Institute, University of Hull)
Prof Peter Osborne (Professor of Advanced Manufacturing – University of Sheffield Advanced Manufacturing Research Centre, University of Sheffield)
Project Description:
Since the 1970s wind turbine blades have been manufactured using discrete composite blades. These blades are a tried and tested technology, both structurally and aerodynamically. Since the formulation of the blade-element momentum (BEM) theory by Glauert, horizontal wind axis turbines (HAWT) have been optimised in such a way that they are now capable of reaching power coefficients of around 0.5 (based on aerodynamic efficiency), which is quite close the to the Betz-Joukowsky’s limit of 0.593 (Porté-Agel et al., 2020).
Though these structures are capable of extracting a lot of energy from the wind, these structures suffer from high cyclic loads and must be reinforced adequately. A major trend in the offshore wind industry is to produce wind turbines with larger rotor diameters. This will inevitably increase the weight of the rotors blades, and gravitational loads will become design drivers. Additionally, as the blades become longer, they will also deflect more, and thus structural stability becomes of increasing importance.
Even though modern turbines are highly efficient at extracting the power from a freestream airflow, the same cannot be said at a windfarm level. Wind turbine wakes are responsible for significant power losses in wind farms. The so called ‘greedy’ turbines within the first row of the array extract more energy from the wind. Leaving downwind wind turbines to suffer from turbulent air, receiving lower wind speeds, and higher fluctuating loads. This not only will produce less AEP but will reduce the life expectancy of the blades.
Wind farm control via yaw or pitch angle actuations has received an increasing amount of attention recently to mitigate wake effects and provide more energy for the whole wind farm. However, due to their limitations in terms of induced unsteady loads and efficacy, they have yet to be implemented commercially. This is why in this project, we propose a new wind farm control concept in which active blade morphing is used to mitigate wakes effects.
Passive and active morphing aerofoil and wings have been an active field of research in the aerospace and aviation industry for several decades (Lachenal et al., 2013). Many of morphing concepts are bio-inspired such as the one based on the common swallow (Nafi et al., 2021). However, there are very limited studies on using morphing technology in wind turbine blades.
The novelty of this projects comes from studying the wake formation of a developed wind-turbine prototype with active morphing blade sections in a wind tunnel environment. Our aim is to assess the aerodynamic performance when changing the geometry of the blade and visualise the wake formation.
Methodology
The project will involve an initial literature review of current active morphing blade technologies, wind-turbine aerodynamics and wake formation.
After identifying the most promising morphing technology considering aerodynamic and manufacturing constrains, the blade will be then modelled on a CAD software, followed by some structural studies and then manufactured using high-precision 3-D printers. The printed sections will be assembled to form the blade structure and its dynamic sections will likely be powered by motorised components and controlled with a single-board micro-controller. We will investigate different geometry changes such as in-plane or out-of-plane transformation. We will also examine in the project the use of different material technologies such as shape memory polymers (SMP), shape memory alloys (SMA) and bi-stable composites.
Once a working morphing blade is developed, this will be assembled on to a small-scale wind turbine model.
The finalised wind turbine model and its wake region will then be tested in the subsonic Durham University Wind Tunnel under various operating conditions. To ensure the scalability of research outcomes to utility-scale turbines, we will follow the guidelines established in the literature to ensure minimum dependence of flow statistics on the Reynolds number and wind tunnel blockage. Further flow measurements will be also conducted in one of the national wind tunnel facilities with a long test section to study complex structure of far-wake region, where downwind turbine are usually located.
References & Further Reading
Lachenal, X., Daynes, S. & Weaver, P. M. (2013) Review of morphing concepts and materials for wind turbine blade applications. Wind energy, 16(2), 283-307.
Nafi, A. S., Krishnan, K., Debnath, A. K., Hackett, E. E. & Gurka, R. (2021) Wake characteristics of a freely rotating bioinspired swept rotor blade. Royal Society Open Science, 8(7), 210779.
Porté-Agel, F., Bastankhah, M. & Shamsoddin, S. (2020) Wind-turbine and wind-farm flows: a review. Boundary-Layer Meteorology, 174(1), 1-59Wang, W., Caro, S., Bennis, F. & Salinas Mejia, O. R. (2014) A simplified morphing blade for horizontal axis wind turbines. Journal of solar energy engineering, 136(1).
Zhuang, C., Yang, G., Zhu, Y. & Hu, D. (2020) Effect of morphed trailing-edge flap on aerodynamic load control for a wind turbine blade section. Renewable Energy, 148, 964-974