
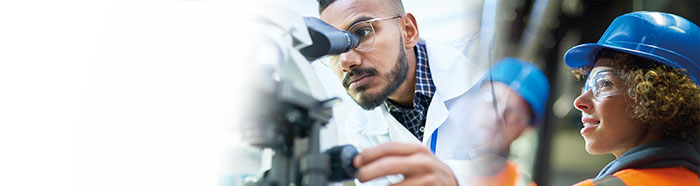
Research projects
- Research area
Achieve a sustainable wind farm life cycle
- Institution
University of Sheffield
- Research project
Low maintenance reliable main bearings for large wind turbines
- Lead supervisor
- PhD Student
- Supervisory Team
Dr Gary Nicholas (Research Associate - Department of Mechanical Engineering, University of Sheffield, University of Sheffield)
Wooyong Song (ORE Catapult)
Siren Tan (Victrex)
Project Description:
This PhD scholarship is offered by the EPSRC CDT in Offshore Wind Energy Sustainability and Resilience, a partnership between the Universities of Durham, Hull, Loughborough and Sheffield. The project is sponsored by industry partner, the Offshore Renewable Energy (ORE) Catapult. The successful applicant will undertake six-month of training with the rest of the CDT cohort at the University of Hull before continuing their PhD research at the University of Sheffield. The project is part of a PhD Research Cluster, Research for optimisation and reliability of wind turbine systems and components.
Almost all the bearings in wind turbine transmissions are rolling element type (1). That includes slow and high-speed shafts, gearbox, blade pitch bearings, and the main bearing that supports the rotor. Wind loading is highly variable and so bearings can operate at changeable speed, high and very variable loading (2). This is a bad place for bearings and there are lots of wear and fatigue failures – design life is 20 years but bearings rarely last that long (3). As machines have got larger, this state has worsened. Manufacturing very large bearings (up to 5m diameter) is expensive and repairing or replacing them very difficult. For example, to replace the main bearing requires the removal of the whole rotor and blades – imagine doing that at sea from a ship mounted crane.
In other large scale machines (e.g. hydro-electric power stations, ships propeller bearing) sliding type or ‘hydrodynamic’ bearings (4) are much more common (e.g. read about Waukesha’s Maxalign bearing https://www.waukbearing.com/en/products/fluid-film-bearings/journal-bearings/tilt-pad-journal/maxalign-bearings.html ).
There is increasing interest from industry to come up with new designs for these kinds of bearing for wind turbine applications. There is believed to be a prototype turbine in China that has operated successfully for a year. Other bearing companies (5) are interested and embarking on similar technologies; see the cute little video, which nicely explains their concepts (https://www.daidometal.com/20220928-2/)
Some of the challenges (6) will be around finding bearing design, materials, and lubricants that will withstand the high loads and start-stop nature of operation. This project is about supporting those developments. Some questions that will need to be addressed: will conventional bearing facing materials survive the extreme conditions, how will lubricant be supplied to the bearing faces in such a large assembly, will greases be adequate, the effect of saltwater contamination, and how will the oil film formation and performance be monitored?
We have industrial support from Victrex (the world leader with 75% market share in PEEK tribological polymer, who will supply test samples), ORE Catapult (will supply wind loading data, and the potential for field trials), Kluber (lubricant manufacturer who will supply WT greases), Waukesha Dover Precision (major bearing manufacturer, who will guide design process and provide samples).
As well as being a member of the Offshore Wind CDT, you would also be joining the Leonardo Centre for Tribology, which is an active and friendly group. There are ~25 PhD students working on machine elements, tribology, lubrication, and sensor systems for wind, auto, rail and energy applications. The group has well equipped labs and its own office space for the PhD students. https://www.sheffield.ac.uk/leonardocentre
Training and development
You will benefit from a taught programme, giving you a broad understanding of the breadth and depth of current and emerging offshore wind sector needs. This begins with an intensive six-month programme at the University of Hull for the new student intake, drawing on the expertise and facilities of all four academic partners. It is supplemented by Continuing Professional Development (CPD), which is embedded throughout your 4-year research scholarship.
The successful applicant will be provided training in tribology, rig design and build, sensor design and signal processing. These will be delivered in house and through peer learning, also using online facilities where available. They will also have access to modules within the Faculty of Engineering (in Sheffield) where relevant.
This research is in a growing area which and can provide strong publications for someone considering an academic career. However, as the research involves extensive design and mechanical analysis activities, this PhD would be an excellent preparation for someone keen for a role in high-technology engineering or consultancy.
Entry requirements
If you have received a First-class Honours degree, or a 2:1 Honours degree and a Masters, or a Distinction at Masters level with any undergraduate degree (or the international equivalents) in engineering, physics, or a related subject, we would like to hear from you.
Recruitment has closed for this project and applications are being assessed for September 2025 entry.
Industry Support
If you have any queries about this project, please contact Prof Rob Dwyer-Joyce, r.dwyer-joyce@sheffield.ac.uk
You may also address queries about the CDT to auracdt@hull.ac.uk.
Watch our short video to hear from Aura CDT students, academics and industry partners:
Funding
The CDT is funded by the EPSRC, allowing us to provide scholarships that cover fees plus a stipend set at the UKRI nationally agreed rates. These have been set by UKRI as £20,780 per annum at 2025/26 rates and will increase in line with the EPSRC guidelines for the subsequent years (subject to progress).
Eligibility
Our funded Doctoral Scholarships are available to UK Students. The advertised CDT scholarships in this current recruitment round are available to Home (UK) Students only as the CDT has reached the annual cap, set by the funding council (UKRI EPSRC), on international student recruitment for the 2025 intake. To be considered a Home student, and therefore eligible for a full award, a student must have no restrictions on how long they can stay in the UK and have been ordinarily resident in the UK for at least 3 years prior to the start of the scholarship (with some further constraint regarding residence for education).
Guaranteed Interview Scheme
The CDT is committed to generating a diverse and inclusive training programme and is looking to attract applicants from all backgrounds. We offer a Guaranteed Interview Scheme for home fee status candidates who identify as Black or Black mixed or Asian or Asian mixed if they meet the programme entry requirements. This positive action is to support recruitment of these under-represented ethnic groups to our programme and is an opt in process.
How to apply
Recruitment has closed for this project and applications are being assessed for September 2025 entry.
Interviews will be held online with an interview panel comprising of project supervisory team members from the host university where the project is based. Where the project involves external supervisors from university partners or industry sponsors then representatives from these partners may form part of the interview panel and your supplementary application form will be shared with them (with the guaranteed interview scheme section removed). Interviews will take place during early and mid-June.
If you have any queries about this project, please contact Prof Rob Dwyer-Joyce, r.dwyer-joyce@sheffield.ac.uk
You may also address queries about the CDT to auracdt@hull.ac.uk.
References
1. https://www.windpowerengineering.com/different-kinds-bearings-used-wind-turbines/
2. Hart, E., de Mello, E., Dwyer-Joyce, R.S., (2022), Wind turbine main-bearing lubrication – Part 2: Simulation based results for a double-row spherical roller main-bearing in a 1.5 MW wind turbine, Wind Energy Science
3. Faulstich S, Hahn B, Tavner PJ. Wind turbine downtime and its importance for offshore deployment. Wind Energy 2010;14:327–37.
4. Frêne, D. Nicolas, B. Degueurce, D. Berthe, M. Godet, Hydrodynamic Lubrication: Bearings and Thrust Bearings (Elsevier, Amsterdam, 1997)
5. https://www.daidometal.com/wind-power/
6. https://www.victrex.com/en/windwhitepaper