
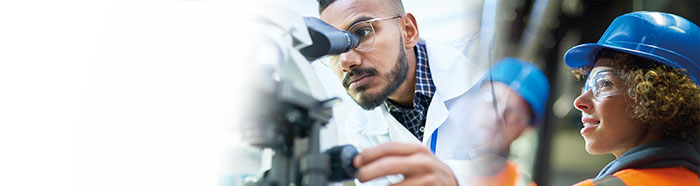
Research projects
- Research area
Next generation materials and manufacturing
- Institution
Durham University
- Research project
Multiscale Design of Fracture and Fatigue Resistant Bio-mimetic Composite Materials for Wind Energy Applications
- Lead supervisor
Dr Stefan Szyniszewski (Assistant Professor, Department of Engineering, Durham University)
- PhD Student
- Supervisory Team
Dr Edward Archer, Senior Lecturer of Advanced Composite Materials, Ulster University
Chris McHugh, Dry Fibre Development Manager, AMRC
Project Description:
The project aims to translate biological structures, such as those in the mother of pearl and abalone sea creatures, to 3D woven composite manufacturing technology. Evolutionary convergent shells exhibit characteristic topologies with interlayered soft and stiff building blocks, allowing them to achieve 1,000 larger fracture toughness than that of the individual building blocks. The mechanism is primarily based on crack deflection.
The goals are:
(1) create a parametric unit cell encompassing the key features of biological topologies,
(2) select and optimise a range of human- made and natural fibres, yarns and matrix materials to emulate biological topologies,
(3) develop a computational model of the 3D woven unit cell and assess its performance against baseline composites,
(4) produce lab-scale demonstrators to experimentally validate crack deflection mechanism and enhanced fracture and fatigue performance.
Methodology
It is envisaged that the research will cover:
- Identification of length scales and parameterisation of fracture and fatigue resistant biological structures.
- Simplified computational models of these unit cells to assess crack deflection and overall fracture toughness performance,e employing multiscale modelling based on cohesive interface and calibrated element erosion criteria for base materials.
- Adapting biological unit cells toward 3D woven representative volume element (RVE), considering orthotropic nature of technical textiles and stochastic variations of geometries and material properties.
- Improving RVE using optimisation approaches to identify the best performing 3D woven topologies.