
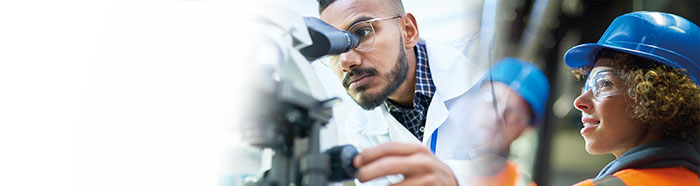
Research projects
- Research area
Big data and sensors and digitalisation for the offshore environment
- Institution
University of Hull
- Research project
Numerical modelling of wind turbine blade manufacture
- Lead supervisor
Professor James Gilbert (Director - Energy & Environment Institute, University of Hull)
- PhD Student
- Supervisory Team
Dr Charlie Lloyd (Leverhulme Early Career Research Fellow, School of Architecture, Building and Civil Engineering, Loughborough University)
Prof Peter Osborne (Professor of Advanced Manufacturing – University of Sheffield Advanced Manufacturing Research Centre, University of Sheffield)
Prof Robert M Dorrell (Professor of Fluid Mechanics, Loughborough University)
Soeren Hendrichson, Siemens Gamesa Renewable Energy
Project Description:
As the understanding of wind turbine manufacture and operational parameters have increased, so has the total length of the blade and complexity of the internal structures. The aim of this PhD is to investigate and model the interaction of these internal structures with the infusion epoxy and quantify its effects on blade manufacture in collaboration with Siemens Gamesa Renewable Energy.
Wind turbine blades are some of the largest composite structures currently manufactured and they are becoming larger and more sophisticated. Blades are manufactured from composites with glass/carbon reinforcement and epoxy resin matrix. The infusion of resin into the blade mould is governed by complex and interacting flow, thermal and chemical processes, some of which are not fully understood. In order to ensure consistently high quality manufacture of existing and new blade designs, it is desirable to create numerical models of the infusion process to better understand and adapt process setup. Working with Siemens Gamesa Renewable Energy (SGRE), the largest manufacturer of offshore wind turbines, we will investigate techniques to model the resin infusion process for current and planned blade designs. The work is supported by SGRE and will involve close collaboration with SGRE colleagues in the UK and Denmark. The project aims are:
- Establish process for generating blade casting simulation models from available CAD and FEA models.
- Investigate key process parameters affecting resin flow and penetration during casting process.
- Model/simulate the casting process and resin flow for a particular blade design based on identified key parameters.
- Develop model scenarios to simulate ‘good’ blade casting as well as various casting defects and compare to ‘real life’ experience.
- Identify key parameters affecting various defect scenarios.
- Optimise casting parameters for maximised quality and consistency.