
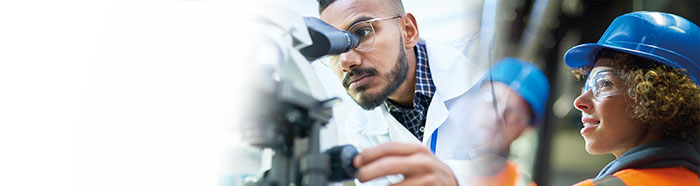
Research projects
- Research area
Big data sensors and digitalisation for the offshore environment
- Institution
University of Hull
- Research project
Wind Turbine Blade Inspection using Machine Learning for Diagnosis of Structural Faults
- Lead supervisor
Prof Nina Dethlefs (Professor of Computer Science (Artificial Intelligence), University of Hull)
- PhD Student
- Supervisory Team
Professor Yiannis Papadopoulos (Professor – Faculty of Science and Engineering, University of Hull)
Project Description:
This project aims to develop a method for Wind Turbine Blade (WTB) inspection using Machine Learning and Computer Vision, that would allow early detection and diagnosis of structural faults in WTBs, aiding in condition-based maintenance (CBM) in the Offshore Wind (OSW) Industry.
At present, the industry relies on the use of manual inspections of blades for fault detection and diagnosis. The use of drones for inspection has been proven for bridges and dams and is in the process of being implemented in the OSW industry [1]. However, current methods of inspection require huge volumes of data and labour-intensive pre-processing.
This project aims to utilise machine learning methods, to reduce human input required in the detection and diagnosis of faults in WTBs. This will consist of developing a set of novel computer vision algorithms that can achieve high accuracies of fault detection and classification from limited datasets, through few/zero shot learning [2] and physics-based grey-box learning
to introduce prior knowledge into the learning process.
The project will develop a novel framework based on the concept of Trustworthy AI that is suitable and safe for use in critical applications, such as OSW, considering the use of a human-in-the-loop system where human involvement is reduced but not negated. This is aimed to address existing concerns around the reliability and explainability of AI models for critical applications and potentially facilitate uptake in the industry.
While this project aims primary to make contributions to fundamental research, as is the nature of a PhD, we will communicate and collaborate with industry throughout, to ensure that the resulting innovation is fit for purpose – tackling the issues of data availability, data quality, and transparency that currently plagues ML-aided condition-based maintenance in the OSW industry [3].
Methodology
Initially, a range of existing approaches, including transfer learning models and few/zero shot models [2] will be evaluated to determine the requirements of a novel system. Tools including SafeML [4] will be applied to the fault detection algorithms to establish a degree of confidence in the reasoning of the algorithms during testing.
Explainable AI principles will be applied using grey-box models [5] that combine prior domain knowledge of physics and environmental conditions faced by turbine blades, with cutting-edge neural image analysis algorithms, such as convolutional neural networks, or vision transformers. We will further consider (deep) reinforcement learning to allow the system to continuously improve over time and learn from human feedback, further increasing the level of human controllability and hence trust.
These methods aim to deliver a reliable decision on the location and type of damage, in order to reduce the level of human input required, allowing supported decision making for O&M planning.
A framework for the application of the techniques developed for industry will also be proposed, based on interaction with stakeholders and industry partners. The framework is intended to be tested on up-to-date inspection data from industry.
References & Further Reading
- Shihavuddin, A.S.M., Chen, X., Fedorov, V., Christensen, A.N., Riis, N.A.B., Branner, K., Dahl, A.B., and Paulsen, R.R. (2019). Wind Turbine Surface Damage Detection by Deep Learning Aided Drone Inspection Analysis. Energies, 12(4).
- Sung, F., Yang, Y., Zhang, L., Xiang, T., Torr, P.H.S., Hospedales, T.M. (2018). Learning to Compare: Relation Network for Few-Shot Learning. Proceedings of the IEEE Conference on Computer Vision and Pattern Recognition (CVPR). 1199-1208
- Chatterjee, J., & Dethlefs, N. (2021). Scientometric review of artificial intelligence for operations & maintenance of wind turbines: The past, present and future. Renewable & sustainable energy reviews, 144.
- Aslensefat, K., Sorokos, I., Whiting, D., Kolagari, R.T., Papadopoulos, Y. (2020). SafeML: Safety Monitoring of Machine Learning Classifiers through Statistical Difference Measures. Arxiv, 10.48550/ARXIV.2005.13166.
- Yang, Z., Eddy, D., Krishnamurty, S., Grosse, I., Denno, P., Lu, Y., Witherell, P. (2017). Investigating Grey-Box Modelling for Predictive Analytics in Smart Manufacturing.