
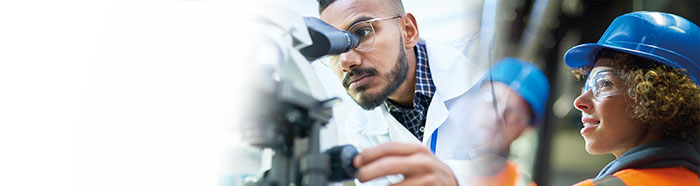
Research projects
- Research area
Physics and Engineering of the offshore environment
- Institution
Durham University
- Research project
Optimisation of the internal structure of wind turbine blades
- Lead supervisor
Dr Stefano Giani (Assistant Professor in the Department of Engineering, Durham University)
- PhD Student
- Supervisory Team
Professor Will Coombs (Professor – Department of Engineering, Durham University)
Project Description:
Modern wind turbine blades are large structures, with complex geometries and they are subjected to a large number of aerodynamic loading cases and design constraints. Many new wind farms are under constructions and many more are planned for the future. In this context the efficiency and reliability of wind turbine blades are paramount.
The focus of this project is to study ways to optimise the structural design of the blades to reduce their weight and increase their reliability. Structural optimisation techniques are frequently used as part of the design process for many applications, but the numerous design constraints that wind turbine blades are subjected makes it a hard problem. Also, the newest designs involve composite materials which add an extra layer of complexity to the problem but also new ways to optimise the design.
Composite materials are characterised by a mesoscopic structure that can be highly customised opening the door to optimisation methods. This project will deliver novel numerical techniques that allow engineers to better design wind turbine blades. In the scope of this project, the methods are applied to blade designs and the results of the optimisation process are analysed and assessed.
References:
T. Adams, S. Giani, W. Coombs (2019), A high-order elliptic PDE based level set reinitialisation method using a discontinuous Galerkin discretisation. – Journal of Computational Physics 379, 373-391.
R. Bird, W. Coombs, S. Giani (2019), A posteriori discontinuous Galerkin error estimator for linear elasticity. – Applied Mathematics and Computation 344-345, 78-96.
R. Bird, W. Coombs, S. Giani (2017), Fast native-MATLAB stiffness assembly for SIPG linear elasticity. – Computers & Mathematics with Applications 74(12), 3209-3230.