
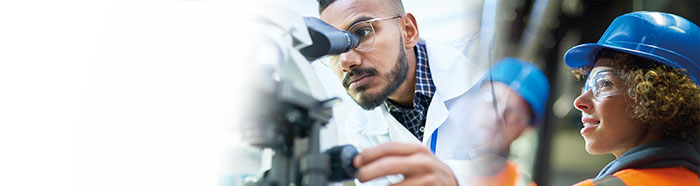
Research projects
- Research area
Accelerate consent and support environmental sustainability
- Institution
University of Hull
- Research project
Sustainable, Low-Cost Recycling of Plastic Transition Piece Covers used by the Offshore Wind Industry
- Lead supervisor
- PhD Student
- Supervisory Team
Dr Martin Taylor (Lecturer in Chemical Engineering, University of Hull)
Project Description:
Wind turbine blade and nacelle parts after manufacture need to be protected during transportation to prevent damage before assembly. They are wrapped into plastic “bags” (polyvinyl chloride (PVC) transition covers). These transition covers are discarded after use, creating environmental concerns, contributing to the global plastic crisis. Ørsted is an international company working on offshore and onshore wind farms. Ørsted has a hub in Grimsby (East Coast Hub), where over 70 tonnes of plastic covers are held in an outside enclosure, with no end of use strategy.
This project investigates environmentally friendly chemical processes to upcycle plastic waste into valuable products (fuels and fine chemicals), using ight as the power source (photocatalysis) and establish a circular economy for offshore wind.
This approach is copied from natural processes, in which plastic materials are decomposed by solar light. These natural processes, though, can take decades, this work aims not only at speeding up the natural decomposition of plastic under light but also to do so in a controlled manner, so that the decomposition reactions can be tailored to give valuable molecules. We will make the “tools” (photocatalysts) that turn light into energy for the controlled decomposition reaction of plastic. The photocatalysts are embedded in the plastic and the resulting composites placed in a liquid medium and exposed to light. The high-value molecules from the controlled decomposition of the plastic leach into the liquid medium, from which they can be extracted. We also aim at studying the conditions of the decomposition reaction towards the optimization of time, yield and sustainability.
The process developed here follows from the funded project “Sunburst” [3751266 Research England] where non-toxic, low-cost iron oxide was used as photocatalyst for the controlled decomposition of PLA and water as the liquid medium in which the high-value monomer, lactide, was released after exposure to UV light. The use of water for PVC has the further advantage of “extracting and storing” chloride, giving a solution of reusable chloridric acid and, at the same
time, avoiding the production of chlorinated organic molecules, considered an environmental pollutant. High-value molecules such as alkanes (fuel and lubricants) were obtained from pure PVC using a UV light, in preliminary studies. We will concentrate on PVC samples provided by Ørsted, who awarded MGF an Innovation Exchange prize (Upcycling Protective Plastics from Offshore Wind Farms; £ 21250).
The focus on PVC waste material from real transition covers, instead of model PVC, will introduce new challenges, such as the identification of additional plasticisers, dyes and other additives and the development of processes to separate them from the PVC, that can then be re-utilised in the photocatalytic decomposition towards high-value products. We also aim at establishing the basis for studying upscaling of the processes discovered so far, moving from milligrams to grams before the end of the project.